VACANCIES AT MERCEDES AMG HPP
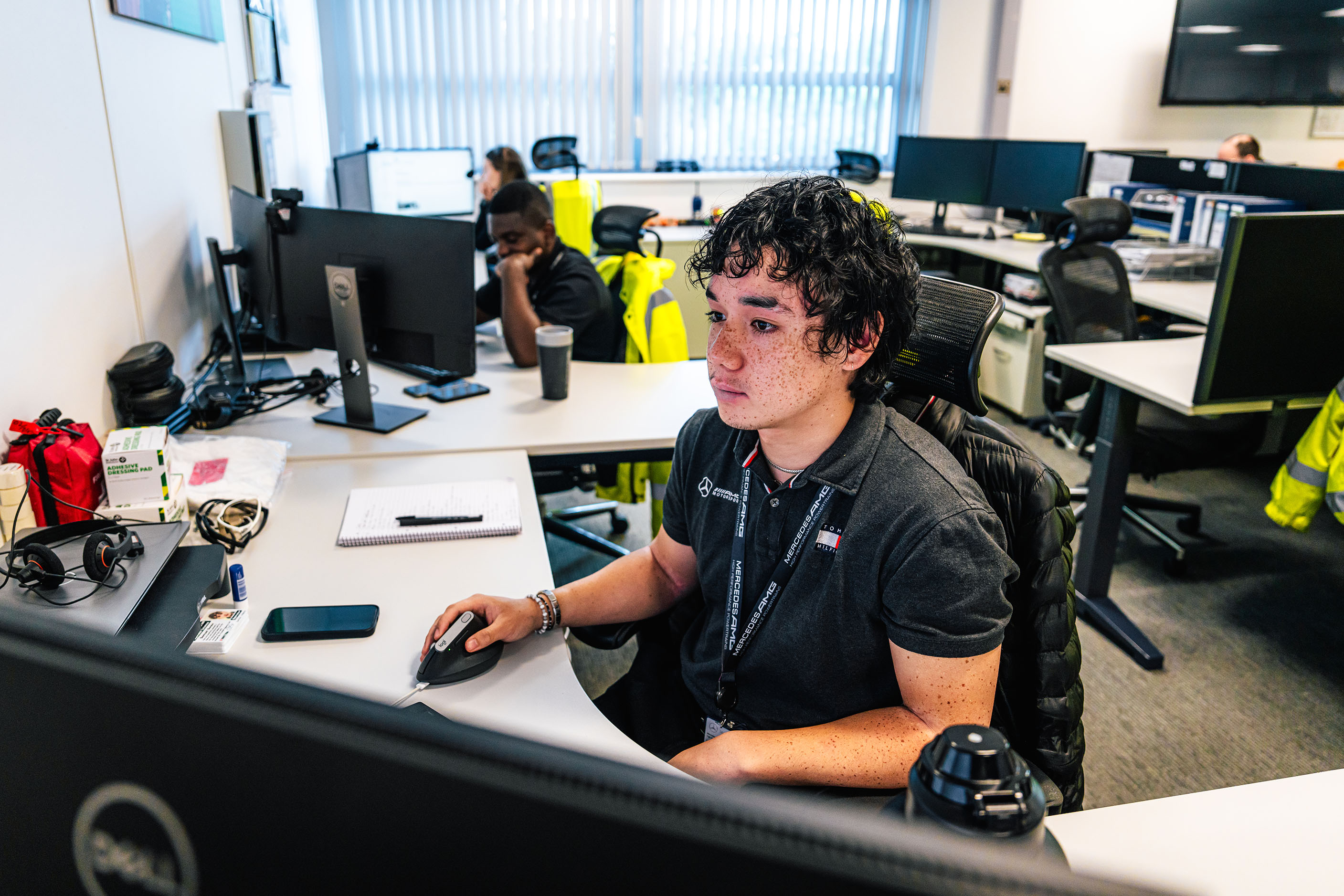
Careers
Early Careers Vacancies
In August we will open our application window for our next intake of Early Careers vacancies! We have over 50 opportunities available, across all disciplines, for exceptional students to join our Eight-time World Championship winning team at our state–of-the-art Technology Centre in Northamptonshire.
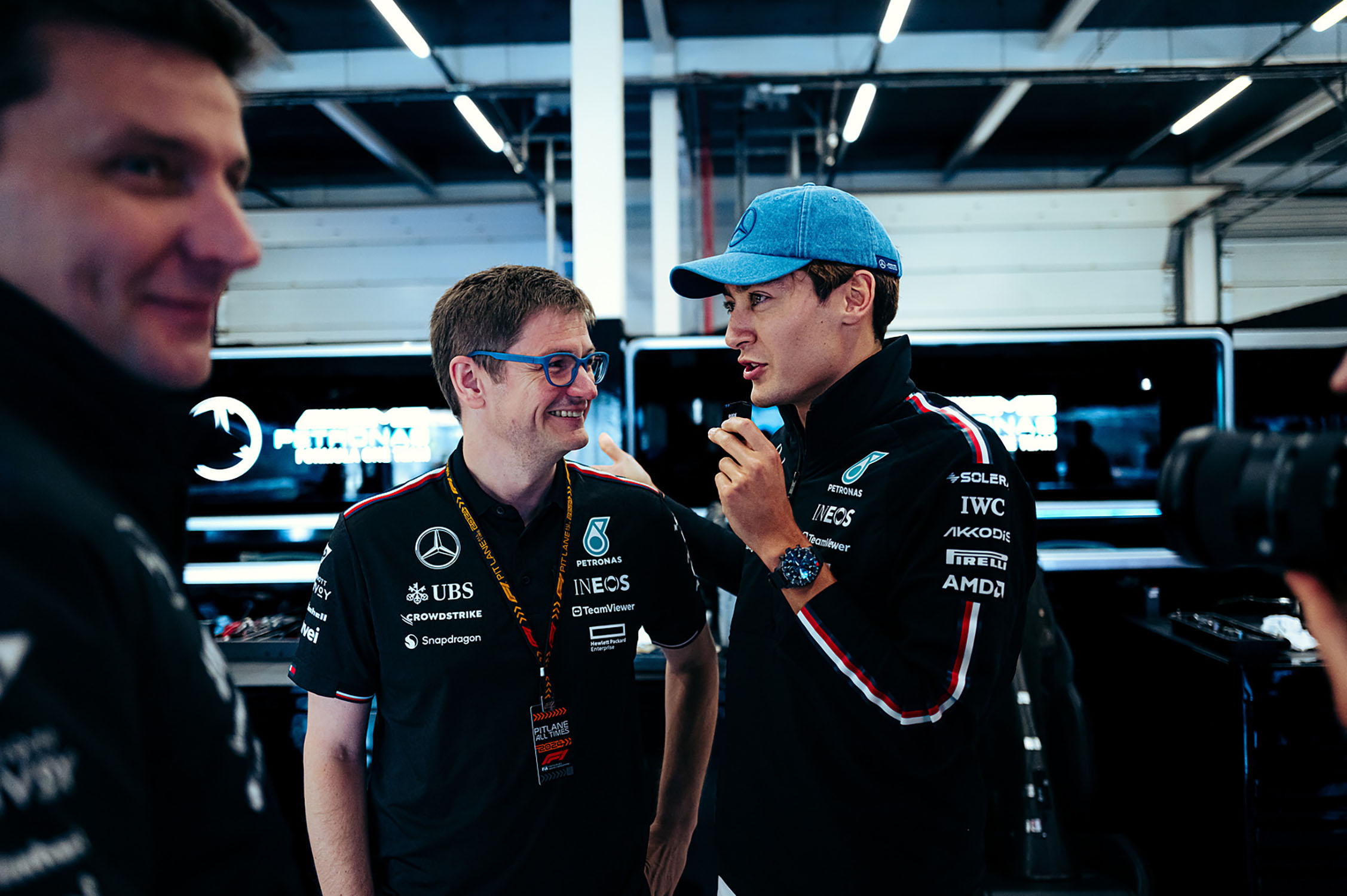
F1 Engineering
What We Do – F1 Trackside Team
Want to find out more about what our F1 Trackside Team do here at HPP, view the video below from Barney our Head of Product Validation to get an in-depth insight into the world of the F1 Engineering.
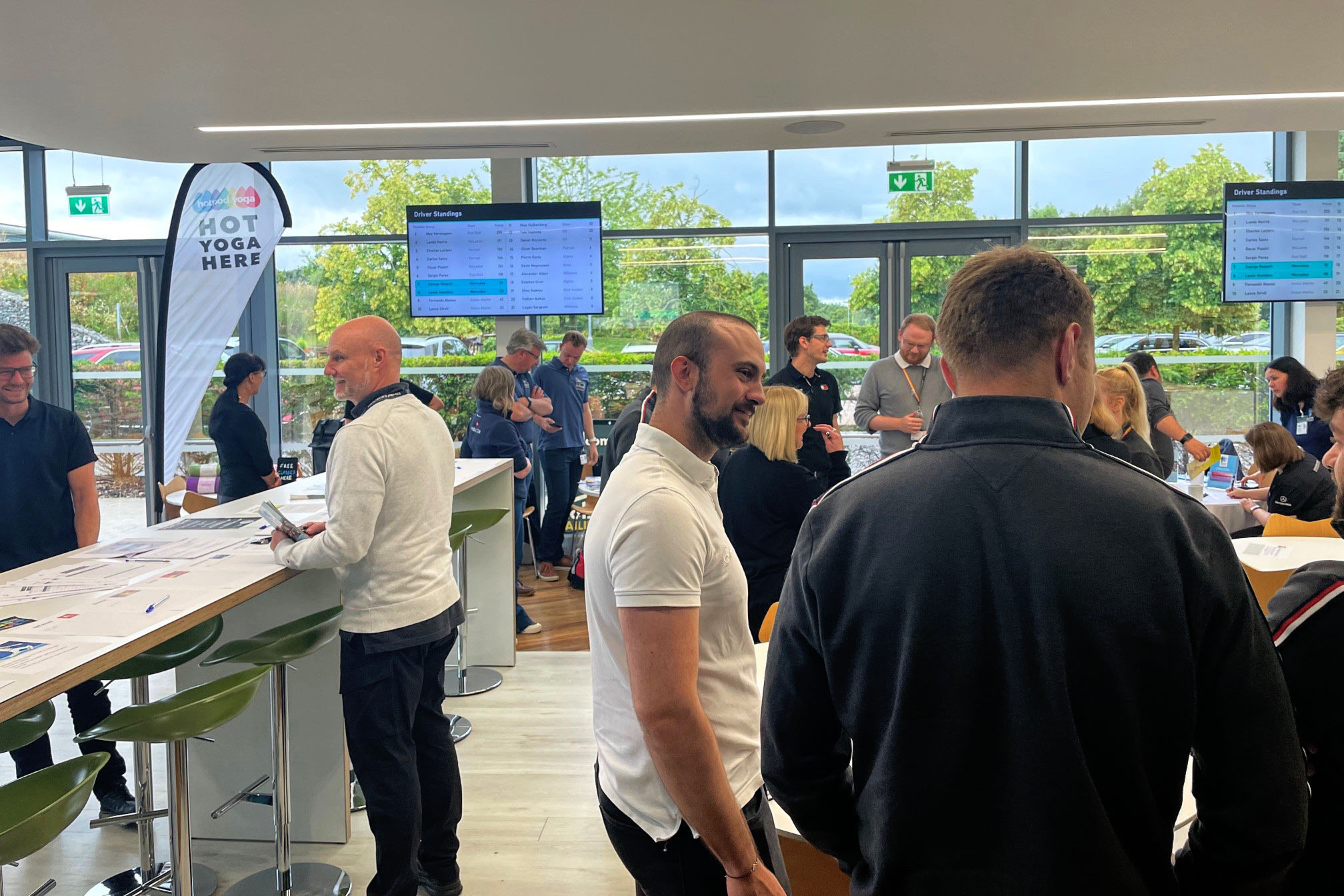
Events
Inclusion Fair
Earlier this month we hosted an inclusion fair where members of our Employee Networks and Project Teams as well as representatives from internal and external groups, networks and clubs such hosted market stalls sharing a variety of activities and sessions available for our employees to join. Creating an environment which is inclusive for all, and […]